

Automakers often assemble battery packs in-house by piecing together battery modules. The other distinct difference in powertrain production is the integration of battery packs.
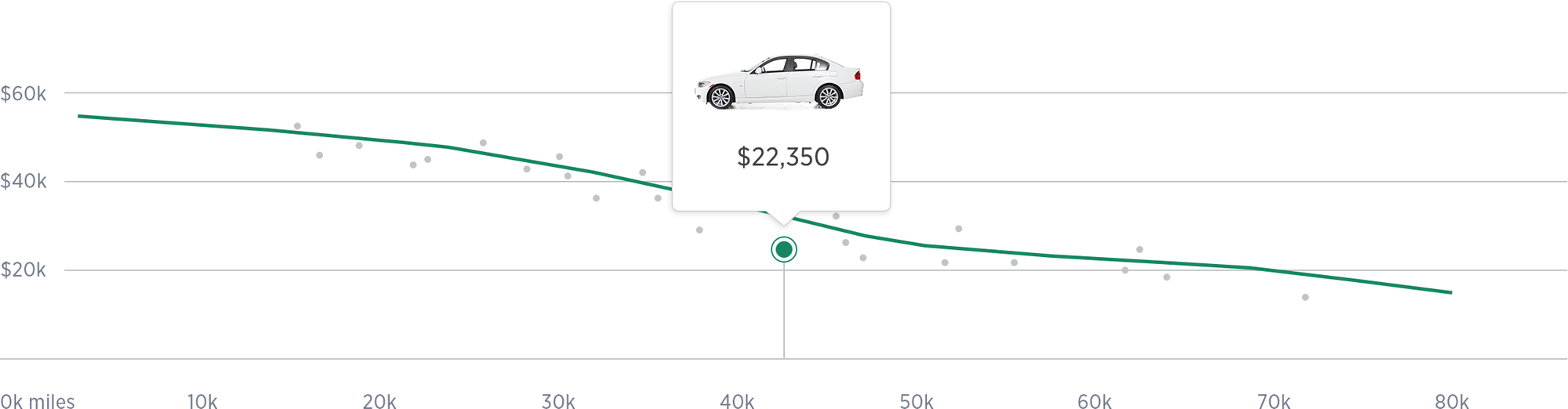
In this sense, the switch to BEV production affects not only OEMs and their suppliers but also producers of machinery and automation equipment for engine-related parts.
#SHIFT CAR SALES INSTALL#
Instead of the elaborate casting and machining processes necessary to make crankcases, cylinders, camshafts, and rods for ICEs, smaller and less complex machining methods can be used to manufacture and install components for electric motors, which include rotor hubs, stator hubs, magnets, and bearings. There are also significant differences in the manufacture of their components. (See the 2018 BCG report The Future of Battery Production for Electric Vehicles.) As a result, this large CPV gap between ICEVs and BEVs is likely to diminish significantly before too long.Īssembly isn’t the only area where production of ICEV engines and BEV motors differs. However, electric vehicle battery costs are declining fast because of improvements in scale, factory automation, and efficiency. All told, BEV specific components increase CPV to 130% compared with an ICEV. Other BEV-specific parts, such as high-voltage wiring, drive up CPV by another 4 percentage points. On top of the price of batteries, the power electronics in a BEV add another 6 percentage points to CPV. This high price tag is mainly rooted in materials, which make up as much as 60% of the BEV battery cost.
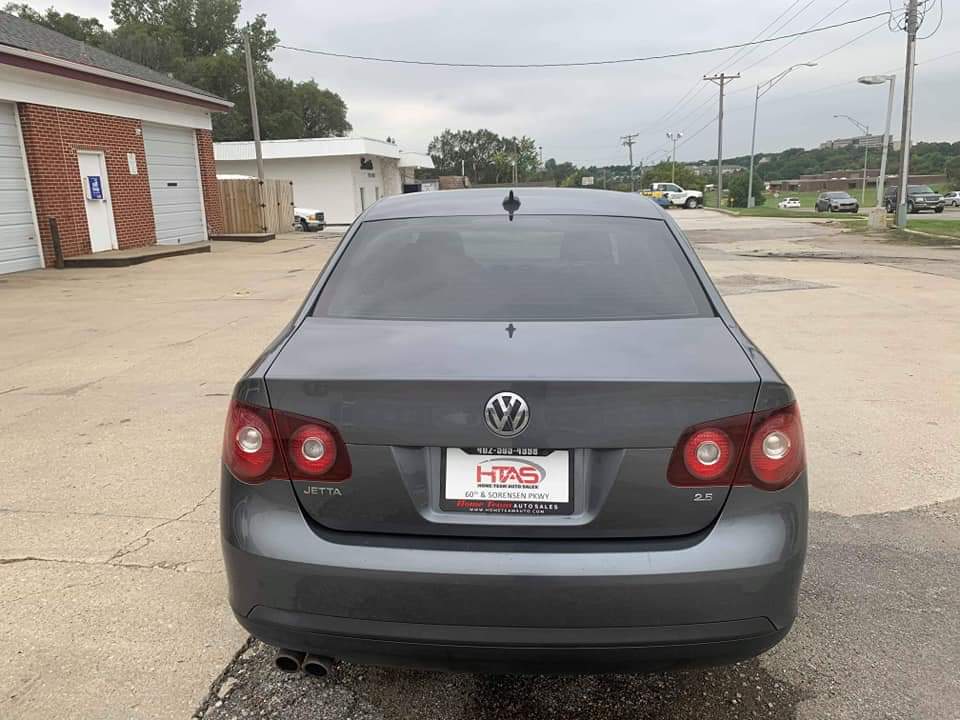
Indeed, the battery system amounts to about one-third of the total BEV CPV and one-half of the total CPV relative to an ICEV. And while those would be eliminated in a BEV, they would be replaced by battery cells, modules, and packs, which are far more costly than an ICEV powertrain.

In ICEVs, the engine and transmission, as well as some auxiliary parts, account for about 31% of CPV. Included, among other things, are DC/DC and DC/AC converters and power electronics controllers. This covers all the equipment essential for running BEVs and electric hybrids but doesn’t exist in pure ICEVs. In addition, the multispeed gearboxes used in ICEVs are virtually always swapped out for a single-speed transmission in BEVs because the power output of electric motors is efficient and consistent across a much broader range of RPMs than conventional ICEs. The battery pack consists of modules that contain battery cells, a battery management system that monitors performance, a thermal management system to cool the battery, interconnects, and housing. They are instead replaced by a battery pack and an electric motor. The main components of an internal-combustion-engine (ICE) powertrain-the engine and auxiliary systems, such as the alternator, starter, and fuel and exhaust systems-are unnecessary in a BEV. These differences can be separated into two categories: powertrain and power electronics. The differences in composition between BEVs and ICEVs will ultimately determine production requirements. To help automakers and suppliers better manage this period of uncertainty and understand what the future may hold, BCG conducted a study on how electromobility (e-mobility) will alter automotive production, with a specific focus on shifts in labor requirements. In particular, workforce deployment will be a critical facet of this transition.
#SHIFT CAR SALES FULL#
Without a full understanding of the repercussions of the transformation from internal-combustion-engine vehicles (ICEVs) to BEVs, automakers will be unable to produce a coherent plan for navigating this consequential shift. There has been plenty of uncertainty in the automotive industry, even before the collapse in manufacturing and sales as a result of the COVID-19 pandemic, much of it centered on battery electric vehicles (BEVs) and how quickly they will gain widespread acceptance.Īlthough it is difficult to predict future sales figures for BEVs precisely, one thing is clear: a combination of increasing demand for more environmentally friendly vehicles and government-mandated reductions in automakers’ fleet-wide average emissions will compel OEMs to increase their share of BEV production to at least some degree.īut often lost in the enthusiasm and anticipation surrounding the emergence of BEVs is the potentially profound impact this product shift will have on the operations of automakers and suppliers-and, by extension, on global employment patterns in the auto industry. The CEO’s Dilemma: Business Resilience in a Time of Uncertainty.Technology, Media, and Telecommunications.
